MontysEvilTwin
Well-Known Member
This may have relevance to a recent thread here. I just bought a HDR-FOX on EBay for £22.49 incl. delivery. Don't get too excited, it has no remote, no hard drive, a couple of dinks in the case, and it does not power up. But I knew this and bought it for spares. I thought the power supply had probably died, but there was no sign of bad capacitors: the power supply is now working fine in another unit. The front panel board is also working correctly. I had a good look at the main board: a component, designated U21 on the board has blown. This is quite close to the power connector, and is tucked away under the hard drive in the bottom left hand corner. Here are some photos:
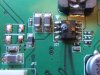
Blown component at U21
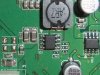
Good component at U21
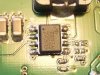
U21 Component showing code
From what I can tell, the component (Z1073A) is a voltage regulator. It is only has eight pins (well spaced out) and I think could be replaced. The most difficult part would be removing it without damaging the connectors on the board: desoldering braid should make this possible. I don't need to fix the board, but I may have a go if I can find somewhere that sells the part in fewer than hundred quantities.
This fault might not be relevant to anyone else: other dead main boards may have completely different failed components, but this could be a common fault. On other dead boards the same component may not have failed so spectacularly, making it harder to spot.
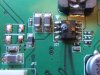
Blown component at U21
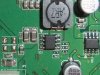
Good component at U21
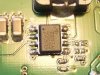
U21 Component showing code
From what I can tell, the component (Z1073A) is a voltage regulator. It is only has eight pins (well spaced out) and I think could be replaced. The most difficult part would be removing it without damaging the connectors on the board: desoldering braid should make this possible. I don't need to fix the board, but I may have a go if I can find somewhere that sells the part in fewer than hundred quantities.
This fault might not be relevant to anyone else: other dead main boards may have completely different failed components, but this could be a common fault. On other dead boards the same component may not have failed so spectacularly, making it harder to spot.