6 years on and I've resurrected this. Needless to say I forgot everything to do with using FreeCAD (or even that I used FreeCAD last time) and practically had to start again. In the intervening period, I haven't had a need for 3D print sufficiently great to warrant the time involved.
I want to fit an externally-accessible HDD power point to my home-brew PC ("ZEN"), to support the eSATA port (not eSATAp – I slipped up there). The only existing commercial solutions (a panel-mount Molex) are expensive and unavailable. My concept is to 3D-print an adapter bracket which makes a normal cable socket panel-mounting.
As just a one-off, I could simply bodge something (probably in less time than I've been buggering around with FreeCAD). However, I have been contemplating the trade-offs between buying a printer and outsourcing (again!). The price has come down, and it's just the sort of thing I could have been playing with during lockdown (it looks possible to build my own, and I really like the Delta type). On the other hand I have a busy enough life (normally) and a 3D printer would likely just sit gathering dust.
The first problem was coming up with a design concept which would be manufacturable. Pressed metal sheet would be ideal, but I have no way to do that. Will a plastic printed part be strong enough to withstand the insertion force and the waggle to unplug? Don't know. A plastic bracket will need to be in two parts, because it needs to locate the Molex using just the lugs so the Molex has to be trapped in, and ideally without having to dismantle the Molex (remove the crimped contacts).
Having mulled that over in the back of my mind for several weeks, I bit the bullet a couple of days ago and went for it. I went back to my 2015 design files to find out what I used then (remembering this thread would have helped). I was driven up the wall by the floor plan drawing being "broken" when I tried to extrude it into the third dimension, despite having chased down the constraints – which turned out to be duplicated lines (how did they get there?).
If you look at a Molex you'll see the lugs are bevelled. I could make right-angled notches ("pockets"), but how to make them bevelled? It turns out the answer isn't "chamfer", but "draft" – in this case meaning (apparently) something like the draft of a boat, and enables any particular face on the 3D model to be assigned an angle off orthogonal.
It didn't help that I am using FreeCAD 0.15 on Win7 whereas the current version is 0.19, so much of the on-line documentation assumes at least 0.18. No, I didn't want to risk breaking everything by updating software! I would have installed the Linux version on ZEN had 0.19 been available in the Mint repo. (Incidentally, it seems like 0.19 is less critical on constraints – so long as areas are "closed", the locations of features are defined by where they are on the drawing, so really there's no imperative on total constraint... although constraints are useful in an engineering situation.)
Anyway, late last night I finally had STL files (manufacturable 3D part models) and was ready to outsource... only to find the maker community hub 3Dhubs has gone commercial only. Fishing around I came up with
Treatstock, which seems to do something similar, and placed an order with a business in Eastleigh for a total of $7.14 inc delivery (Treatstock seems to work in USD only).
My parts are small, so it is hard to compare this price with the cost of my 2015 print, but certainly it suggests there is no economic argument for having my own printer (although it might be justified on other arguments, such as hobby value).
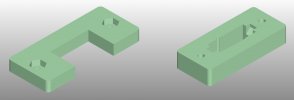